There’s always something putting pressure on security budgets. Lately, it’s tariffs. Last year, it was inflation. Before that, supply chains, chip shortages, labor gaps, the list goes on.
But underneath all of that, a bigger question is surfacing across the industry: How do we manage the systems we already have, over the long haul, with the predictability and visibility teams actually need?
That’s where lifecycle management steps in. And honestly, it’s where more of our attention needs to be.
Lifecycle matters now more than ever
It’s easy to focus on the project: the install, the go-live, the punch list. That’s the visible part. But most of the real work and the real cost happens after that.
Security systems are expected to run for years, across multiple buildings, shifts, stakeholders, and budget cycles. And yet, a surprising number of organizations treat lifecycle planning as an afterthought.
We’ve all seen it: the site where half the cameras are failing and no one’s sure which ones are still under warranty. The access system can’t be updated because the server OS is three versions behind. Or the quote that balloons because no one realized how far gone the infrastructure really was.
That’s what happens when lifecycle planning is an afterthought. And the further along you get, the more expensive the cleanup becomes.
It’s about less chaos
Lifecycle planning is not a new idea. Most of us have been doing some version of it for years. The problem is that it’s rarely systematic. Too much lives in email threads and tribal knowledge. And as teams shift and systems sprawl, that makes it harder to stay ahead of issues that shouldn’t be surprises.
Most teams have some version of lifecycle planning in place, but let’s be honest, it’s often informal. Details get lost in inboxes, spreadsheets go stale, and a lot of the institutional knowledge walks out the door with the last guy who managed the system.
That’s when the headaches start. Suddenly, no one’s sure what equipment is where, which systems are nearing end-of-life, or what should’ve been updated six months ago. And when something breaks, it’s a scramble, not because the fix is complicated, but because no one saw it coming.
These aren’t exotic problems. They’re basic maintenance issues that become costly because no one has a clean line of sight.
The longer view pays off
Let’s not kid ourselves, budgets aren’t getting looser, and the pace of change isn’t slowing down. But that’s exactly why lifecycle thinking matters. It allows us to stretch the value of existing systems without running them into the ground.
When you know what’s still working, what’s fragile, and what’s next in line, you don’t have to replace everything all at once. You can phase it. Prioritize it. Time it in a way that doesn’t wreck operations or blow the budget.
That’s not just smart planning. That’s good risk management.
Tariffs are going to come and go. So will product lines, manufacturers, and budgets. But lifecycle management, the boring, necessary, unglamorous part of this business, is what gives teams the ability to stay focused, stay operational, and stay ready for whatever comes next.
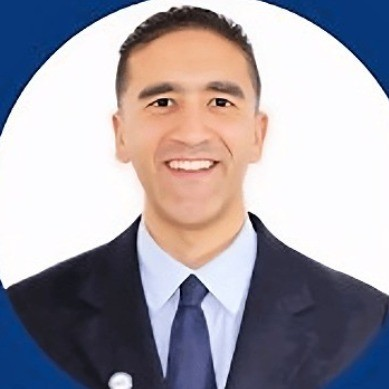
David Santiago
David is a Physical Security Professional and SiteOwl contributor. From his service in the U.S. Marine Corps to leading campus-wide security initiatives, David brings deep operational insight. When not writing or consulting, he enjoys tai chi, playing basketball, and chasing the perfect beach sunset with his family.