Manufacturing facilities face a unique set of security challenges. From protecting valuable equipment to ensuring worker safety and regulatory compliance, the stakes are high. With sprawling sites, complex supply chains, and increasing cyber-physical threats, physical security leaders are rethinking their strategies to adapt to a rapidly changing landscape.
As we look ahead to 2025, manufacturing security is undergoing a transformation. The focus is shifting toward integrated systems, cutting-edge technology, and proactive approaches that enhance efficiency while addressing both traditional and emerging risks.
Here are the key trends shaping manufacturing security in 2025 and how they can help physical security leaders stay ahead.
1. Physical security integration will continue to take priority
Gone are the days of siloed systems. Manufacturing facilities are adopting integrated platforms to unify their security operations. By connecting video surveillance, access control, intrusion detection, and operational tools, security teams gain a centralized view of their entire facility and improve operations, among other advantages.
- Improved situational awareness: A unified view of all security systems enables faster response times.
- Enhanced efficiency: Centralized management streamlines operations and reduces complexity.
- Data-driven insights: Advanced analytics uncover patterns and optimize security protocols.
- Cost savings: Eliminates redundant systems and minimizes manual intervention.
As AI, IoT, and other advanced technologies continue to gain momentum, the future of manufacturing security lies in leveraging these integrated systems to create smarter, more connected environments.
2. The rise of AI-driven physical security
While 90% of organizations are using AI-assisted tools for cybersecurity, only 22% have implemented AI-driven measures in their physical security operations. This number is expected to increase significantly as businesses realize AI’s potential to revolutionize security practices and improve efficiency.
Early successes and case studies are already paving the way for broader adoption, showing tangible results in reducing risks and improving efficiency. By 2025, AI is poised to play a critical role in manufacturing security, with applications such as:
- Perimeter Security: AI-powered systems monitor factory perimeters, distinguishing between weather events, wildlife, and genuine threats. This reduces false alarms and ensures faster, more accurate responses.
- Warehouse Monitoring: AI analyzes video feeds to identify safety hazards like blocked emergency exits or workers entering restricted areas, helping to improve workplace safety.
- Equipment Protection: AI tracks high-value equipment, detecting unusual movements or usage patterns to prevent theft, tampering, or unauthorized access.
These examples highlight just a fraction of AI’s potential in physical security. In the years ahead, manufacturers can expect greater adoption of AI, unlocking innovative use cases and reshaping how facilities protect their operations, assets, and personnel.
3. Security drones will transform manufacturing surveillance
Drones are quickly becoming a critical tool for facility security, providing aerial views and access to hard-to-reach areas. In a 2023 industry survey, 35% of manufacturing companies reported plans to integrate drones into their security and surveillance operations within the next two years.
Autonomous drones offer significant advantages by following predefined patrol routes or responding dynamically to triggers such as motion or alarms. They can cover up to 50 times more ground in the same timeframe as traditional patrols, all while delivering high-definition video feeds in real time.
Specific Applications in Manufacturing:
- Inventory Management: Drones equipped with RFID readers can scan and track inventory in warehouses, improving efficiency and reducing errors.
- Safety Inspections: Drones can inspect hazardous areas or confined spaces, minimizing risks to human workers.
- Environmental Monitoring: Drones can monitor air quality, detect leaks, and identify potential environmental hazards.
While the advantages of drones in manufacturing security are clear, challenges persist. Regulations governing drone use and privacy concerns remain key hurdles, alongside logistical complexities in deployment.
Despite these obstacles, the benefits far outweigh the drawbacks. As drones become more advanced and accessible, their role in manufacturing security will continue to expand, helping companies achieve safer, more efficient operations.
4. The role of cloud technology will continue to grow
Cloud technology is reshaping how manufacturing facilities manage their security systems, offering unprecedented flexibility, scalability, and cost-efficiency. Over 90% of companies now utilize some form of cloud-based infrastructure, with 76% adopting multi-cloud strategies to leverage the strengths of multiple service providers.
For manufacturing security teams, cloud-based platforms provide a centralized solution for monitoring and managing operations across multiple sites, all from a single interface. These systems enable seamless coordination across facilities, making them indispensable in modern security operations.
Key Applications in Manufacturing Security
- Video Surveillance: Cloud-based systems store and analyze footage from multiple cameras across various locations, improving monitoring, incident investigation, and response times.
- Access Control: Centralized cloud platforms allow teams to manage employee access, visitor permissions, and security protocols across facilities with ease and consistency.
- Supply Chain Security: Cloud solutions track goods throughout the supply chain, reducing theft, ensuring accountability, and safeguarding valuable assets.
- Lifecycle Management: Platforms like SiteOwl provide real-time oversight of security assets, including maintenance schedules, vendor management, and system health monitoring, all in one place.
By leveraging cloud technology, manufacturing facilities can enhance security, reduce operational complexities, and stay agile in an increasingly competitive landscape.
5. The rise of proactive security lifecycle management
As manufacturing facilities become more reliant on advanced security systems, lifecycle management is emerging as a critical focus for physical security leaders, and for good reasons.
Managing security assets—such as cameras, sensors, and access control systems—throughout their entire lifespan ensures optimal performance, reduces downtime, and minimizes costs.
With budgets tightening, proactive maintenance will take center stage. Facilities can no longer afford to rely on reactive approaches that fix issues only after they occur. Lifecycle management tools, like centralized asset management platforms, allow security teams to schedule preventive maintenance, track system performance, and oversee vendor activities in one place.
Key Benefits of Physical Security Lifecycle Management
- Extended Asset Lifespan: Regular maintenance ensures that security systems remain operational for longer, protecting initial investments.
- Reduced Downtime: Proactively addressing issues prevents system failures that could compromise security or disrupt operations.
- Cost Efficiency: Identifying and resolving minor issues early avoids expensive replacements or repairs.
- Improved Compliance: Lifecycle management ensures systems are consistently updated to meet industry regulations and safety standards.
Manufacturing leaders are also leveraging these platforms to coordinate vendor activities, such as installations and service calls, ensuring transparency and accountability across all maintenance processes. With lifecycle management, security teams can maintain a higher level of reliability while staying prepared for future challenges.
Preparing for the future of manufacturing security
Technology will play a pivotal role in shaping the future of manufacturing security. Integrated systems, AI, drones, and cloud platforms are already driving innovation, with even greater advancements on the horizon.
Lifecycle management will be central to this transformation, ensuring security systems operate efficiently, reliably, and cost-effectively. By adopting these trends and investing in smarter solutions, manufacturing security leaders can mitigate risks, enhance safety, and optimize operations.
Ready to modernize your security strategy? Download SiteOwl’s free ebook, Securing Your Manufacturing Facility, to learn how to streamline and future-proof your operations.
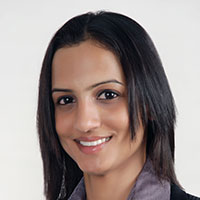
Su Subburaj
Su is SiteOwl's CMO and leads all marketing and communications. Su has extensive strategy and management consulting experience and previously consulted for 3Sixty Integrated where she gained an in-depth understanding of digital transformation challenges in the physical security industry. When not working on strategies to expand SiteOwl's footprint, Su enjoys bad karaoke, weightlifting and traveling.